
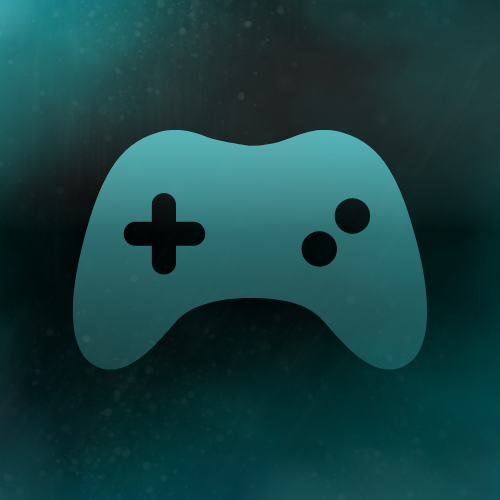
Exactly, it’s just regular old enshittification.
Exactly, it’s just regular old enshittification.
While I’m sure the obvious systemic issues contribute to not looking for alternatives, that does sound like largely an issue inherent to optical pulse oximeters. Engineers aren’t miracle workers, they can’t change physics to their liking.
I’m sure pulse oximeters now are more accurate than they were 20 years ago. The fact we’re still using them is because no alternatives have been found which are as easy to use, reliable, and non-invasive as pulse oximeters, even with the known downsides.
Repository: a collection of computer code for a software program (or app if you insist).
Fork: a copy of a repository so you can edit it without affecting the original.
Pull request: a request to the owner of a repo to bring in some changes you made in a fork.
I think I even got the word count down.
I didn’t test other values but they’re probably OK.
Excellent work, thanks for the laugh.
I find it difficult to lay the blame with VSCode when the terminology belongs to git, which (even 7 years ago) was an industry standard technology.
People using tools they don’t understand and plowing ahead through scary warnings will always encounter problems.
Did you tell him you guess you have to stop doing non-web development then? Clearly you’re not qualified if you can’t have the corresponding title.
You can very safely remove the “probably” from your first sentence.
Libre Office
What the crap kind of washing machine do you use that’s 20 storeys tall?
That sounds like a problem from using too small of a drive. Every torque curve I’ve seen for brushless DC or AC servos is constant torque from 0 to about 75% rated RPM, and then starts to drop off.
Well, that’s why you use a proper servo drive. Yes, technically they oscillate at standstill, but it’s so little it literally does not matter. Closed loop servo control is a solved problem unless you’re trying to implement it yourself.
I don’t know why you’re getting down voted. You’re correct, steppers are used due to cost.
I disagree with all your points. What kind of servos are you talking about?
BLDC and AC servos maintain full torque at stop too, and have about 2-3× the torque of a stepper of similar size.
The only way a stepper can rival a servo for precision is with a high degree of microstepping, which is far from guaranteed positioning with open loop control.
I haven’t directly compared response time between steppers and servos, but I would be extremely surprised if there’s a significant enough difference to worry about. Most servo-controlled machines are larger and so are designed to accelerate slower than a printer, if that’s what you mean. This is intentional because inertia is a thing you have to worry about, not because the servo reacts to command changes slowly.
There are valid reasons steppers are used on printers, but it’s not because they have superior performance.
Cost is the short version, yes.
I don’t know what kind of servos everyone here is talking about that are less precise than open loop steppers. Low quality hobbyist stuff, I guess? Proper servo motors & drives are the standard for good reason for robotics, industrial CNC machines, and pretty much everything else that needs powerful motors with high precision. Much higher power density, higher RPM (good for increasing torque with a gearbox), equivalent or better precision, plus closed loop control is a huge capability and safety gain.
That said, good, industrial quality servo motors are 1) expensive and 2) aren’t made in small enough sizes to be comparable to the steppers on most 3D printers. Even the smallest industrial servo + drive I’ve seen is about 5x as big as the steppers on a personal 3D printer and costs $800ish. Obviously, both are deal breakers for a personal 3D printer.
3D printers are a fairly ideal application for steppers. The moving parts are small and light, meaning you both don’t need a large motor and the danger of slippage is lower. Plus, steppers are cheap.
NFTs do not solve the problem of proof of ownership. Nor can they. If someone steals it from you - whether by trickery, force, or any other means - it’s just as lost to you as any other stolen thing, digital or physical. (Not to touch on the fact that NFTs to date have just been URLs to web hosted media, i.e. ridiculously non-unique and insecure.)
Also, your whole paragraph about theoretical NFT replacement for DRM is just describing a different kind of DRM.
Every credit card company charges large fees to the service provider for charge backs. It’s standard practice. This is also leads to service providers straight up perma-banning customers who initiate charge backs instead of resolving a dispute with the provider.